
It is based on the extrusion process where heated thermoplastic filament is “selectively dispensed through a nozzle or orifice”. Thus, by varying the infill density, there is a reduction in the impact strength of the printed specimens.įused deposition modeling (FDM), is an additive manufacturing (AM) technology used for printing three-dimensional part.

The impact test experimental data establishes that impact strength is directly proportional to the infill density. The highest Charpy and lowest Izod strength found to be 4.72 kJ/m 2 and 1.7 kJ/m 2. The varying infill density specimens weigh lighter as compared to single infill density, which saves the raw material.
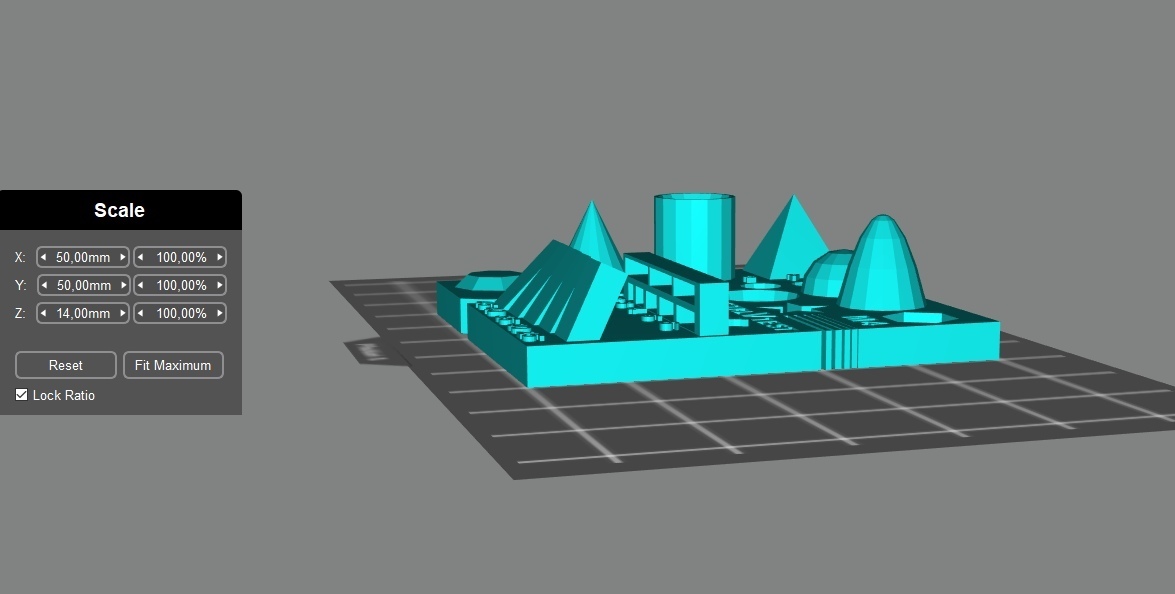
The results demonstrate that the specimens with varying infill density exhibit better tensile strength than the specimens with single infill density. The tensile strength with the highest value of 46.3 N/mm 2 and the lowest value of 29.9 N/mm 2 are found. A computerised tensometer and impactometer used to conduct the tensile and the impact strength of the PLA specimens. The tensile and impact test specimens are printed according to the DIN EN ISO 527-2, ASTM D256 (Izod) and ASTM D6110 (Charpy) respectively. The objective of this study is to investigate the effect of variable infill density on the tensile and impact strength of polylactic acid (PLA) specimens printed by an open-source 3D printer. The set process parameters during FDM printing, affect the mechanical behaviour of the built part. Fused deposition modelling (FDM) is one of the additive manufacturing technique, widely accepted due to its ‘easy to use’ technology.
